2019 Winner's story
Winner's story: Stephen at Honda
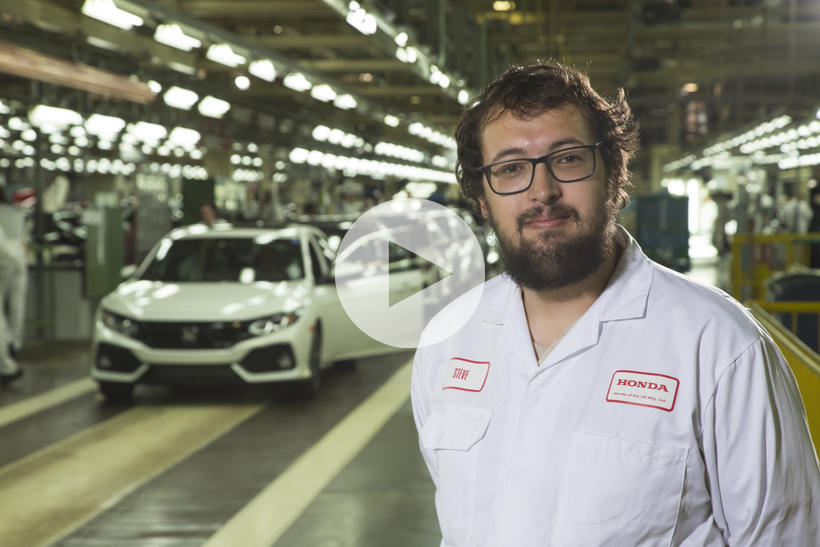
The Autocar Courland Next Generation Award is intended to give its winner a varied experience of Britain’s automotive industry and that is best typified by the contrast between the first and second work placements of 2017 winner Stephen Crossley.
After his inaugural month at the sole factory of supercar maker McLaren, in Woking, he travelled 64 miles down the M4 to Honda’s plant in Swindon – one of more than 30 Honda factories worldwide. McLaren hand-built 3340 supercars in 2017. Honda UK pumped out 166,228 Civics. “The cultures were certainly different,” says Oxford Brookes University student Stephen. “At McLaren, I was with engineers, who have a deadline to meet and do what’s necessary to hit that. At Honda, everybody starts at the same time, wears the same uniform and leaves at the same time.” However, before reaching Swindon, Stephen stopped off at Honda UK’s head office in Bracknell. There, he worked with the team who go to dealerships to check that they’re meeting Honda’s high standards and that they’re able to get the right stock. Then he moved across to customer care. “I was surprised at how much Honda values loyalty,” Stephen says. “If your car is out of warranty but you’ve owned lots of Hondas, they’re often willing to help out.” Assignment three was with the press relations team, assisting at the hectic Goodwood Festival of Speed. “I spent time with journalists,” says Stephen, “and Nick Robinson from Honda R&D Americas, who was demonstrating an NSX. He’s a vehicle dynamics engineer, focusing on ride and handling. That’s the field I’m interested in, so it was very inspiring to chat to him”. Soon after came the press launch of the fifth-generation CR-V in Austria. “We looked after journalists and were on hand with facts about the car,” Stephen says. “It was fascinating to see how things are done. It was a friendlier atmosphere than I expected, while still being professional.” Next, Stephen found himself at Honda Swindon, an enormous plant that handles global production of the Civic hatchback and Civic Type R and three types of engine. “I was with the project engineering team,” Stephen says. “They examine issues that arise and determine whether it’s how the car has been built or a design fault. If it’s the former, they work outwhether it’s a problem with the factory or the suppliers. They also check with other factories to see if the fault is unique to them. And if it’s the latter, they go back and discuss it with Japan. “When I was there, they were trying to find out whether an old problem involving a noise from cars’ fuel return pipe at very low temperatures remained. The factory has a machine that can freeze a car to -30deg C or heat it to 80deg C, so they put it at -5deg C and then listened for this noise on the test track.” Stephen was incredibly impressed by the intensity of Honda’s product checking – in part due to the fact that his personal car is a Leyland-built MG Midget. Part of the process is initial quality study, or IQS. “They take random cars from the production line, inspect them for things like scratches and the harmony between the paint colour on panels, and then drive them on the test track to look for things including wind noise, rattles and loose trim,” Stephen says. “They complement this with a shaker rig, which can simulate real-world tracks." There usually isn’t much to worry about. When I quiz an IQS member on the worst thing he has ever seen, it takes him a minute to recall the world-shattering event of a piece of rear-view mirror trim dislodging over pavé. The most recent transgression has been line staff not catching a thread in the Type R’s gearknob, meaning the ball could be unscrewed. The experience with a mass manufacturer has proved valuable for Stephen. “I got to experience everything Honda does in the UK,” he says, “none of which I’d ever looked into or known about before. “It was really interesting to see how a car company on such a huge scale functions, from dealing with the customer right back to dealing with parts suppliers. “It has given me a good perspective. I’ve always wanted to eventually start my own engineering company, so it’s great experience to allow me to understand all the things that need doing.”
The journey starts here: 2017 Winner's story - Stephen at McLaren
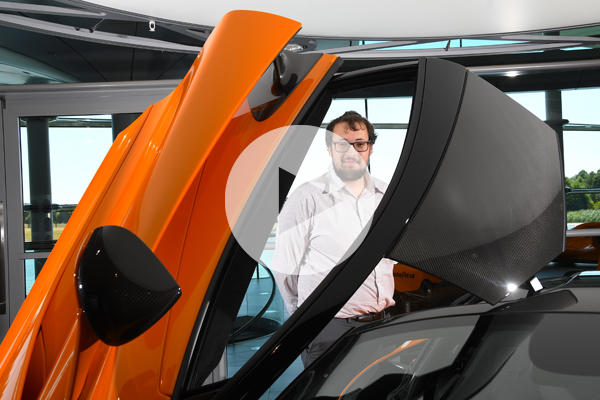
You would be forgiven for thinking that Stephen Crossley had gone straight into full-time employment at McLaren since being declared as the most recent winner of the Autocar Courland Next-Generation Award. That’s because the Oxford Brookes University automotive engineering student has been on placement deep inside McLaren Automotive’s Technology Centre in Woking for the last month. Whereas some work experience placements might involve making the tea and carrying out menial tasks, Stephen has been entrusted with working on top-secret projects in tandem with McLaren’s brightest and best engineers.
Stephen was declared the winner of the contest to unearth and nurture young talent in the automotive industry after Tom Lingard, the would-be victor, sportingly stepped aside due to other commitments. The idea that earned Stephen the prize of industry work placements at some of the UK’s leading automotive companies and £9000 is an active camber system for high-performance versions of road cars. Stephen’s idea was that a car’s camber could be adjusted without changing the chassis or suspension wishbones. His system could enhance the handling and reduce tyre wear, and could bring about road-holding benefits akin to those provided by four-wheel steering, which is now becoming more commonplace on driver’s cars.
Stephen’s passion for improving performance cars made McLaren the perfect destination for his first month of Next-Generation Award work experience. Being the consummate professional, though, he won’t (or rather can’t) tell us exactly what he did at the MTC – because he was working on a system for a McLaren model that doesn’t even exist yet. What he can tell us, however, is that he was surprised by the level of responsibility he was given during his time with the Woking-based firm. “I didn’t expect to be put on anything that could influence a real vehicle, but I was given a project that could tax me a little and could help McLaren,” says the 22-year-old. “I worked on a project to improve the road cars, which was very interesting. It’s always good to see your ideas in practice with an end goal.” And what was the high point of his month at McLaren? “Going out in a Senna,” he says without hesitation. “That was fun. McLaren takes the cars out to a test track on a shakedown, to make sure everything fits properly and the cars work as they should with no rattles. “After my ride in the Senna I was wondering how I could quickly make the £750,000 I’d need to buy one.” And the biggest challenge? “Trying to make something that’s usable for the McLaren engineers. Everything has to be done correctly, explaining what it does clearly.” It seems as if Stephen was a natural fit during his time at McLaren, then. “I’ve always been good at thinking ways around a problem and taking a different route, and I’ve always been persistent,” he says. “When you’re teaching yourself a new software it’s easy to just give up. Cutting through that so you’re able to make something good or useful at the end is key.”
Stephen’s mentor during his stint was Geoff Grose, McLaren’s chief engineer on its Sports Series models. “We’re always looking for people with the right technical ability and aptitude, plus the ability to integrate in a team. To have all of that and really care about the product goes a long way,” says Geoff. “Stephen fitted in well. We put him in the chassis team because of the nature of his award-winning project, and it was an easy fit. We put him in a team that gave him the best exposure to an area where careers would be open to him.” Even Geoff is not allowed to talk in detail about what Steve worked on, but he says “it related to a vehicle’s lift function. It involved computer modelling and test work, so was a nice test for the four-week timescale. He engaged with the project and the team around him really well. He did some good work for us and learned about the career options.” Stephen is off to a flying start, and that’s only the first of his work placements. Next, he is heading to Honda UK, we’ll find outhow get's on next month
Josh at Toyota
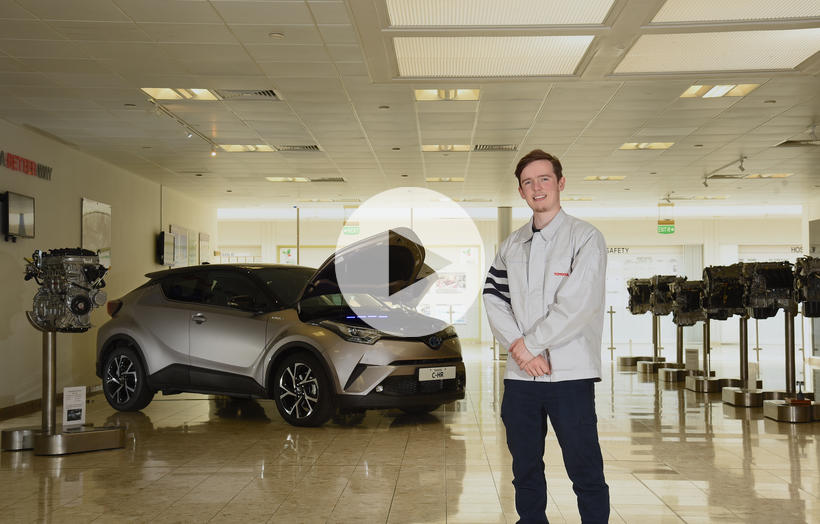
Josh de Wit has been on an incredible journey. Roll back to November 2016 and the University of Sussex student was waiting on stage at the Society of Motor Manufacturers and Traders annual dinner in front of a host of industry experts, wishing for his name to be called out as the winner of the Autocar-Courland Next Generation Award.
Josh did scoop the top prize, and with it he won £9000 and one-month work placements at McLaren, Jaguar Land Rover, Peugeot, Honda, Nissan and Toyota. Now, eight months later, he has just finished his final placement with Toyota and is about to return to university with a wealth of industry experience under his belt. “It’s made me realise exactly what I want to do,” Josh says. “I want to stay in this industry, and it’s been so great seeing all aspects of it.”
Josh has spent the past four weeks working with the product marketing team at Toyota. Based at the Japanese firm’s GB headquarters in Epsom, Surrey, he has been working on everything from car brochures to online marketing, as well as meeting agencies that work with the brand to create car ads. His main objective, however, has been to research connected car systems. “Manufacturers such as Tesla, Mercedes and Audi are moving on very quickly with implementing smartphone connectivity into its cars,” Josh explains. “So I’ve been analysing and evaluating how they do it, and how Toyota can consider its own approach. “This will also ultimately all help develop autonomous driving features, and that’s an exciting thing to be looking into.”
Although Josh’s main interest lies in engineering, he has enjoyed the challenges presented to him in the Toyota marketing team and is grateful for having gained similar experience at other manufacturers. “The research was difficult,” Josh says. “But when it comes to car sharing and autonomous driving, this research will be crucial, so motivation was easy to come by. “People want convenience – that’s what I discovered in my market research. They want their smartphones fully integrated into their vehicles. Streaming music, using sat-nav, having apps showing live parking availability and fuel prices are all important.”
Josh clearly enjoyed his work, and had the chance to present his findings in front of the product marketing team. “It was really helpful getting their views. They’re an awesome team to work with – really fun and supportive,” he says. But, just like all of his other placements, Josh’s experience at Toyota was not confined to the office. He also spent time at the Toyota Motor Manufacturing (UK) factory in Burnaston to see how a car is physically put together through different manufacturing processes. The likes of the Avensis and Auris are made at the Derbyshire facility.
When we meet to discuss his time with Toyota, Josh is wearing a hard hat and high-vis gear after getting shown around Toyota’s engine plant in Deeside, north Wales. “Places like this are the bread and butter of the industry,” Josh says. To fully round off his experience and help immerse himself in what the Toyota brand stands for, he also had a Mirai hydrogen fuel cell vehicle Josh hopes to make the most of his new skills after university loaned to him for three days. “It was so interesting to experience a hydrogen-powered car. I was impressed with how refined it is,” Josh says. “If the infrastructure can catch up, hydrogen has good potential as a fuel of the future.”
Now that his placements have come to an end, Josh will return to university for his final year of study in mechanical engineering. “There are so many positives I can take from the Autocar-Courland Next Generation Award,” he says. “Along with all the practical skills it’s given me, it’s been great making so many contacts. It’s opened so many doors. “It’s allowed me to get used to working at different companies, understanding the time and effort that go into these products, taking them from concept through to production and then to selling them.
“I’m looking forward to studying for another year and continuing my development, but it’s been hugely helpful having this real-world experience. It’s helped give me the edge over other undergraduates, and I wouldn’t have had it without the Next Generation Award.”