2019 Winner's story
Value added to the max
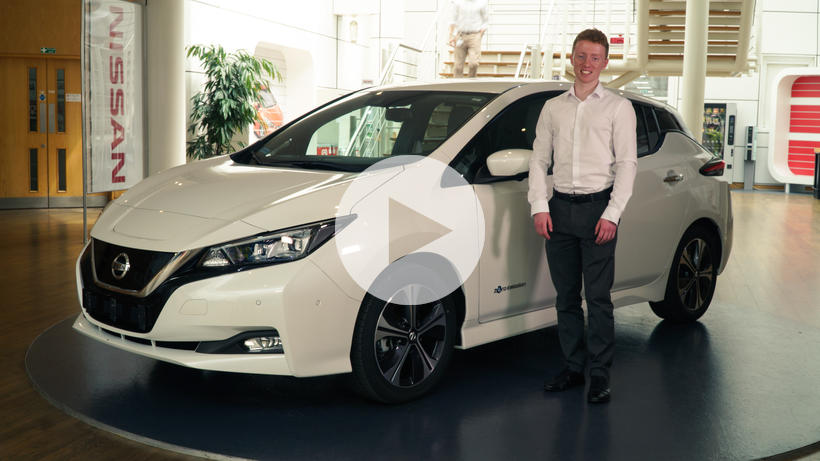
Autocar-Courland Next Generation Award winner Lewis Campbell is at the end of his Nissan placement, during which he learned valuable lessons in R&D, he tells Harry Roberts...
For some, Nissan’s presence in the UK is represented solely by its Sunderland super-factory, where a Qashqai, Juke or Leaf rolls off the line every two minutes. But when Autocar-Courland Next Generation Award winner Lewis Campbell was sent to spend a month working with the Japanese car maker, he was directed towards the lesser-known Nissan Technical Centre, an R&D facility in Cranfield, Bedfordshire, that is responsible for major development work on the Qashqai SUV and Leaf EV. We’ve caught up with Campbell, now at the end of his second of five four-week placements he received as a result of winning the competition, to find out what he’s been up to at Nissan.“It’s been a million times better than I could have imagined,” grins the mechanical engineering student. “I never thought I’d be able to see all the different elements that make up a brand with a global outreach as great as Nissan’s.” Campbell spent most of his four weeks with the value engineering team, a branch of R&D that, as he explains, aims to “give more value to the customer by adding new features or re-engineering a part to make it more efficient”. More specifically, Campbell has been working with the exterior electronics department, which has responsibility for anything found on the exterior of a car that is electronically operated such as wing mirrors, wipers and cameras. According to exterior systems senior engineer Nicholas Jones, Campbell was able to “take an idea that we already had for a changeable part, do the critical engineering and development work with the supplier, manage the timing plan, look at costs and technical feasibility and then bring it to the point where we’re now ready to deliver that onto the car”. This commendation of Campbell’s performance virtually mirrors comments he received during his first placement at McLaren Automotive. “We gave him a real technical problem to solve,” says Jones. “We asked him to use critical thinking and technical ability and he’s really showcased his potential.”Jones added his team has been “very impressed” and that Campbell has a “real critical eye for detail. His ability to work not only as part of a team but also individually with suppliers is second to none.” However, it wasn’t all plain sailing for the student whose anti-cloning registration identification device won him the Next-Gen Award. When asked about the struggles he’s faced over the past four weeks, Campbell says: “I actually feel like I’ve been really challenged. On the first week there was a lot of information to absorb; I was pretty nervous about coming but the team have been so good to me and whenever I needed advice they were always there and always made time for me – I never felt like a chore to anybody.”Jones also took the time to take Campbell to the Sunderland facility. “It was awe-inspiring,” says Campbell. “Getting a tour of the place and seeing the cars starting as a few pieces of pressed metal to 15 minutes later rolling off the production line as a completed car was insane. I felt like a kid in a candy shop.”Campbell has also visited the company’s Paddington-based design studio, a facility responsible for penning the Juke and Qashqai concepts. “Being in the rooms where some of the most recognisable Nissans today were designed was such a cool experience,” he says. But it was a trip to Bedfordshire’s Millbrook Proving Ground that impressed Campbell beyond all else. Given its undulating corners, formidable suspension-testing surfaces and high-speed challenges, Campbell inevitably relished the experience. “Getting to go up to Millbrook and put a couple of different Nissans through their paces was something that I never expected I would get to do through this competition,” he beams. “It was amazing and I loved every minute – I’ll remember that forever.”Campbell’s positivity is a testament to his continued drive and desire to further develop himself and his automotive knowledge, and he admits he didn’t want his time at Cranfield to end. “From day one I felt like part of the team,” he says. “At any point during my time here I felt like I’ve been able to speak to anybody in the building about anything – I was on first-name terms with everybody.“There are so many roles that I had no idea even existed until I got here. Value engineering is now definitely an area I have a far greater appreciation for and is undoubtedly something I’d consider a career in.” Next, Campbell is off to Toyota UK’s head office and will also spend a few days at the manufacturer’s Burnaston factory, which is where we’ll catch up with him again.
Woking nine to five
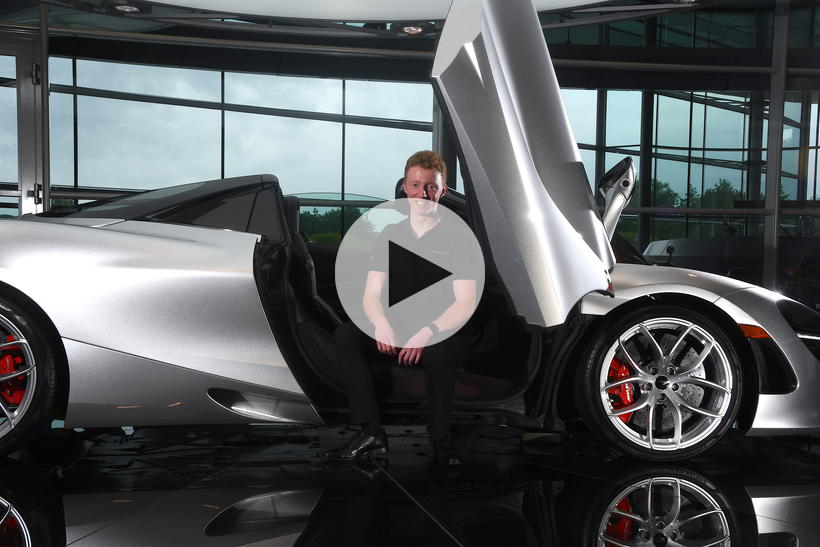
We catch up with the 2018 Autocar-Courland Next Generation Award winner Lewis Campbell as he rounds off a four-week work placement at McLaren’s Technology Centre
You’d have to be made of stone not to feel moved by the shimmering brilliance of McLaren’s Norman Foster-designed Technology Centre in Woking. Even after a month working behind the sweeping glass walls, 2018 Autocar-Courland Next Generation Award winner Lewis Campbell says: “This place is amazing; you come in here and as soon as you walk through that front door, you’re inspired”.
Mechanical engineering student Lewis has spent four weeks with the supercar maker’s electrical systems team, in the first of five work experience placements he won for his idea to revolutionise car registration with an anti-cloning identification device. McLaren’s head of vehicle development, Geoff Grose, says the department’s focus on connectivity and futureproofing was perfect for Lewis because “there’s a lot of stuff he knew about already, so he could make a contribution there from day one”.
And make a contribution he has. In just one month, Lewis has independently carried a project all the way from the proposal stage to having a fully functioning proof of concept installed on a vehicle. “That’s absolutely unheard of anywhere else”, he grins. The rapid turnaround was possible, Lewis thinks, because “you’re only a stone’s throw away from someone in this building who knows exactly what you need if you get stuck”. He adds: “So, although I’ve been working on it fairly independently, there was a lot of input from the team to help me progress with it, which has been absolutely fantastic.”
Unsurprisingly, Lewis is sworn to secrecy about the exact nature of his assignment, but it’s what he’s learned over the course of his placement that really stands out for him. Keen engineer and genuine car guy that he is, he has made the effort to explore Woking’s gleaming corridors and mesmerising workshops, with an access-all-areas pass allowing him to track the stages of a new vehicle’s life, from initial conception right the way through to final assembly. “It’s been really interesting to get an insight into those processes,” he muses, “because, quite honestly, I had no idea how much went into it until I got here.”
Despite his quite obvious flair for problem-solving, Lewis is quick to admit that vehicle electronics “was not his strong suit” before joining McLaren. “I was a bit nervous about that, coming in,” he says, but fortunately it didn’t take much to bring him up to speed; on his first day, a crash course with electric systems manager Liam Sill “started off with the basics, and by lunchtime we were discussing high-level architecture”.
Lewis’s background in mechanics and vehicle systems helped him hit the ground running, but he was lucky to have tutors as keen as him for the placement to be a success. Geoff says that when assigning a trainee to a department, he strives to find a mentor “who is really up for that extra little bit of challenge to ensure they have a great placement”. The benefits of parallel development are evident - Lewis and Liam have already developed a strong rapport. And the electrics expert is clearly impressed with his mentee’s attitude and work ethic: “He’s been in the office till late with the rest of the guys. We’ve given him quite a few challenges to be honest, and he’s shown himself to be very, very capable.”
Indeed, at no point does Lewis imply that he’s been out of his depth during the placement, which is testament, not only to his impressive knowledge and adaptability, but to his willingness to make the most of this golden opportunity. “When I first started working on the project here, I presumed that it would just be writing a report”, he says, “but the speed at which things move at McLaren is amazing”. Evident in his sustained enthusiasm is the company’s commitment to nurturing future talent, and ensuring the training its trainees receive is unparallelled in terms of insight, hands-on experience and potential for contribution.
But such forward-thinking devotion to education and technology is not to be taken as a dismissal of McLaren’s past successes. Lewis says his morning stroll past the facility’s mind-blowing heritage collection, comprising icons like Ayrton Senna’s 1988 F1 championship-winning MP4/4, “never gets old”. “There’s never a day you come in here and you think ‘I wish I was back in bed’”, he says. “Every time you come in that door, you just want to get stuck into your work.” Geoff agrees: “I think the heritage of the brand gives us a kind of common framework to work in. We all would naturally be competitive, we’ll naturally think about what’s going to give the best performance in our products.”
Lewis will now travel to Nissan’s Cranfield Technology Centre to spend four weeks working with the firm’s body, exterior and CAD engineering team. We’ll catch up with him again at the end of his second placement.
Six months of dream jobs
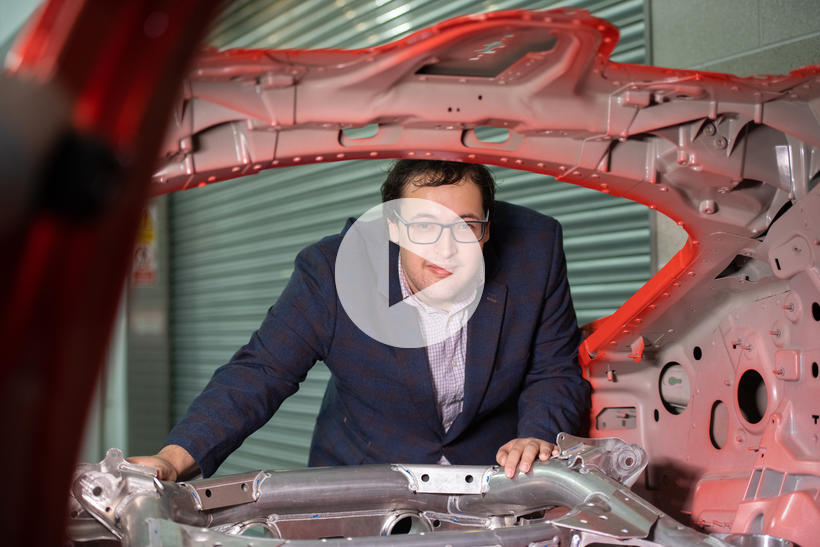
Winner Stephen Crossley has spent six months working with industry leaders, finishing at Jaguar Land Rover. He tells Kris Culmer what he has learned After six placements at major automotive companies, experiencing every important facet of the industry, 2017 Autocar-Courland Next Generation Award winner Stephen Crossley has emerged a wiser man. His final period has been at Britain’s biggest car manufacturer, Jaguar Land Rover (JLR). Here, he has worked in the research and development team, based at Warwick University. “Coming up with new ideas, working on them and then justifying them, selecting which would be best,” is how Stephen neatly sums it up. In fact, he is incredibly impressed at just how many development projects are ongoing at the company.“The centre has facilities for developing technologies such as artificial intelligence, augmented reality and human-machine interface,” he explains, “as well as research on connected and autonomous vehicles, and on smart mobility.” JLR’s use of virtual reality (VR)particularly surprised him. He showed Autocar around JLR’s ‘VR Cave’ in Gaydon, wherein you can walk around and view cars in 3D form, enabling the mind-bending experience of standing inside a Range Rover Evoque and putting your head straight through the dashboard to see the workings of the steering column – very useful if you’re trying to improve packaging efficiency or see how a car’s design looks from multiple angles. Human-machine interface proved particularly interesting: how cars should be as easy as possible to interact with, and know a little about you, so as to improve convenience and safety. “This is something that’s only going to go further and further as we move to autonomous vehicles,” Stephen says. “The biggest improvements would be if you were able to operate functions with minimal distraction and if the car could predict your actions.” Further excitement came from JLR’s development of printable, flexible electronics. “This allows you to place electronics to optimise tighter packaging and weight distribution,” Stephen explains. “It’s also lighter and cheaper to produce, so there are huge benefits.” All of Stephen’s work was theoretical, but it could very well be used in a practical application. “It would be amazing to see a feature on a JLR model in the future and know that I had been there while the concept was in the early research stage,” he says. Indeed, he believes the most valuable skill he learned is how to turn an idea into an innovation. And that’s pretty useful, he says, grinning, because “this all started with me having an idea”. The project he contributed most to concerned the thermal management of components. It involved exploring mechanical and thermodynamic solutions, which, Stephen felt, was perfectly suited to his skillset as an automotive engineering student. It meant evaluating materials and finding mechanical solutions and methods of protecting from environmental factors. Software he used went from the very basic level of evaluative Excel spreadsheets through to computer-aided design (CAD) and modelling platforms, to look at how the project could be taken forward and compare various ideas. Stephen enjoyed what he calls a “collaborative environment” at JLR. “It’s a team effort,” he says. “Tasks are assigned. Then there’s a meeting to find the best solution and how it can work with everything else. Cars are incredibly complex things. You can fix a problem, but the solution may well impede on something else.” “From day one, Stephen got stuck into the project and didn’t look back from then,” says Alex Mouzakitis, JLR’s head of electrical, electronics and software engineering. “For us, bringing in young talent is perhaps of the most important benefit. People like Stephen will come in with fresh ideas and challenge what we do, how we do it and why we do it. So although he has been here for only a short time, the experience that we get from having him is invaluable. “I’ve been in the privileged position of handling the Next Generation Award for three years now, and every year it has been a great year for us.” Reflecting on his time in the Next Generation scheme, Stephen says: “It has been a very informative, interesting and enjoyable experience. I’ve learned a lot and I’m going to go back to university and do things differently and really work toward some end goals that I’ve developed. “I’ve had a look around all these companies and found all these fields I really like, specific areas I want to work in and places I want to go. It has also been really valuable to see what tools are actually used in the industry. But the best thing has been that I’ve found that I really enjoy working in the field, which is brilliant for any student, because there’s always that little bit of doubt. “I’d therefore thoroughly recommend it to anyone.”